PID control of heater with Mitsubishi PLC
We introduced how to control PID control using PLC earlier, but this time, we will use Mitsubishi PLC to introduce how to control the heater PID. PLC used FX3UC and temperature uptake used FX2N-8AD.
Contents
- 1 Capture the current temperature to be controlled into PLC
- 2 Temperature control of heater using PID dedicated instruction
- 3 Set the required constant for PID using auto tuning
- 4 Temperature control of the heater based on the current temperature to be controlled
- 5 Merits and disadvantages that control the temperature of the heater with PLC
Capture the current temperature to be controlled into PLC
The current temperature needs to be taken into the PLC to perform temperature control. This time, the thermocompression (K) eight lines were connected to FX2N-8AD and the current temperature was entered. You need to get into the PLC. This time, the thermocouple (K) was connected to KV-NC4TP and the current temperature was input.
Temperature control of heater using PID dedicated instruction
Temperature control of the heater is performed based on the current temperature to be controlled. Since there is a dedicated instruction called [PID] for PID, use it. [PID] Instructions are auto-tuning functions, so constants will also be set automatically.
Set the required constant for PID using auto tuning
[PID] has an auto tuning function, so set the parameters required for auto tuning and perform auto tuning.
Parameters required for auto tuning
· Measurement value: Current value of control target (temperature this time)
· Setting value: PID control target value
· Sampling time: Period to calculate PID
After setting the parameter, turn on the auto tuning start flag
ON auto tuning start flag to start auto tuning.
When auto tuning is complete, the flag is turned off. The necessary constants are automatically stored in PID.
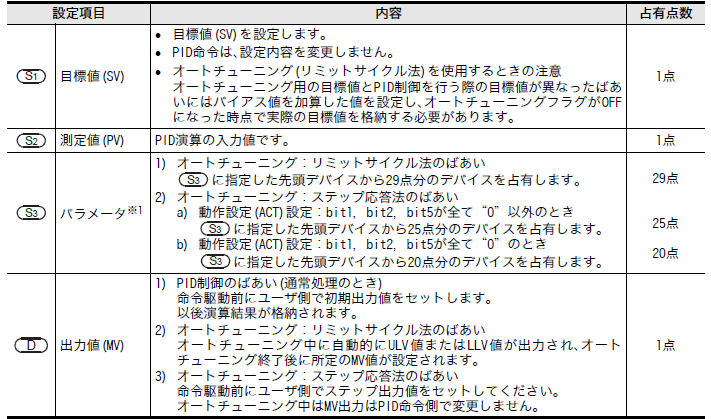
Temperature control of the heater based on the current temperature to be controlled
If the PID constant is determined, actually perform the temperature control of the heater with PID control.
[PID] calculates the output operation amount by PID, and turns the output operation by the PID control cycle with the output operation amount.
Merits and disadvantages that control the temperature of the heater with PLC
Following control examples in the previous key energy, this time we introduced an example of Mitsubishi PLC.
Although there are some differences in PID control instructions and parameters, the merits and disadvantages when PID control is performed is the same regardless of the PLC.