PID control of heater with keyence PLC
When performing temperature control of the heater, it is common to use a dedicated temperature controller (such as E5CC), but if the heater to control increases, it is also necessary to have a temperature controller, and it is also very difficult to arrange it on the board. It becomes. This time, we will introduce how to use the PID control of the heater using the key energy PLC. PLC used KV-N40, temperature capture used KV-NC4TP.
Contents
- 1 Capture the current temperature to be controlled into PLC
- 2 Temperature control of heater using PID dedicated instruction
- 3 Set the required constant for PID using auto tuning
- 4 Temperature control of the heater based on the current temperature to be controlled
- 5 Merits and disadvantages that control the temperature of the heater with PLC
Capture the current temperature to be controlled into PLC
The current temperature needs to be taken into the PLC to perform temperature control. This time, the thermocouple (K) was connected to KV-NC4TP and the current temperature was input.
Temperature control of heater using PID dedicated instruction
Temperature control of the heater is performed based on the current temperature to be controlled. Since there is a dedicated instruction such as [PID] and [Pidat] for PID, use it. I do not know more about PID, so I do not know more, but [Pidat] has an auto tuning function, so the constant will also be set automatically.
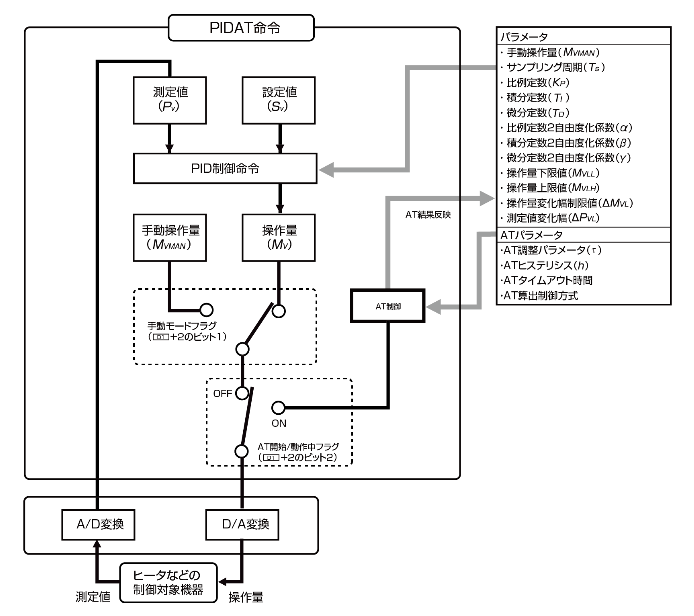
Set the required constant for PID using auto tuning
[Pidat] has an auto tuning function, so set the parameters required for auto tuning and perform auto tuning.
Parameters required for auto tuning
· Measurement value: Current value of control target (temperature this time)
· Setting value: PID control target value
· Sampling cycle: Period to calculate PID
· AT adjustment parameters: Adjust whether "stability" or "fastness" of PID constant by auto tuning
Once the meter is set, turn on the auto tuning start flag
ON auto tuning start flag to start auto tuning.
When auto tuning is complete, the flag is turned off. The necessary constants are automatically stored in PID.
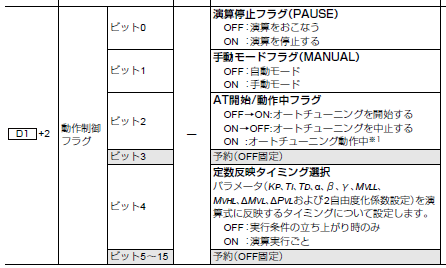
Temperature control of the heater based on the current temperature to be controlled
PIDの定数が決まったら実際にPID制御でヒーターの温度制御を行います。
In fact, the temperature control of the heater is actually performed with PID control.
[Pidat] calculates the output operation amount by PID, and turns on the time-out time according to the amount of operation. You can use the instruction called tpout to convert the output operation amount to pulse output. In fact, the control cycle is specified and outputs only the time according to the output operation amount.
Temperature waveform with PID control and ON / OFF control
The next graph is a set temperature of 45.0 ° C, and the temperature waveform with PID control and ON / OFF control is graphed. PID control used a constant auto-tuned at 45.0 ° C., and ON / OFF control was set to 1.0 ° C hysteresis. On ON / OFF control, it can be seen that the setting temperature is exceeded, and then the vicinity of ± 1 ° C of the set temperature is up and down. In PID control, the temperature is gradually heated to the set temperature, and then it is stable at the same temperature as the set temperature.
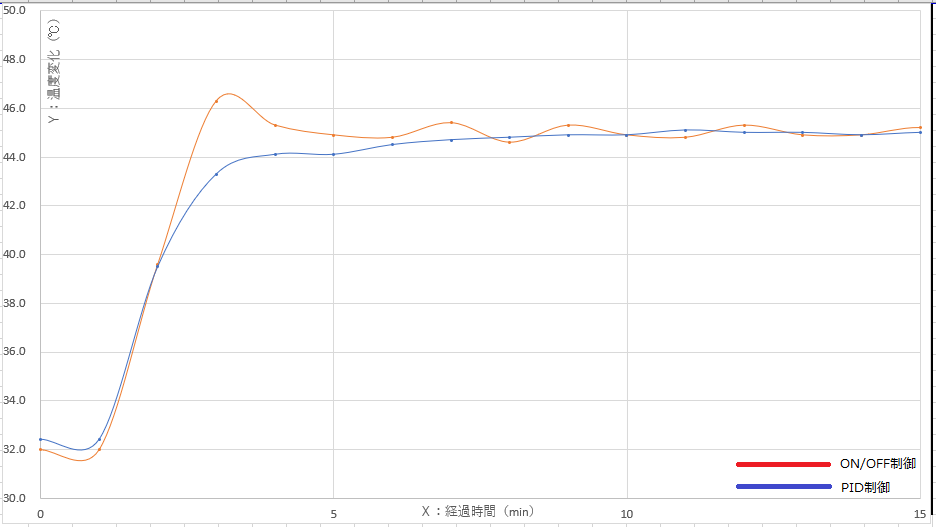
Merits and disadvantages that control the temperature of the heater with PLC
Merit
· No temperature controller is required (advantageous as the heater to control)
· Automatic data collection and management can be performed with PLC
· Graphs collected data with display instruments such as touch panels and display
Demerit
· Design load of control program is large
If there are multiple heaters to be controlled, the benefits of controlling the temperature control of the heater in PLC in consideration of the purchase cost of the temperature controller and the number of wiring steps, etc. By eliminating the need for a temperature controller, the temperature controller is not usually installed on the control panel, so the board is also clear.